Summary of our achievements in 2024
Last year showed amazing progress as we pivoted from the original design that was test flown in November of 2023. While the vehicle performed very well on the ground (up to 125 mph! – an unofficial world record for a flying car), and flew very well as an aircraft during the final flight testing, we didn’t hit our flight speed goal of 160 mph. We could have stopped and put that model into production, but we had set the bar and have taken funds from people with the promise of a high-performance vehicle in both modes, so we kept our integrity and revised the vehicle to meet the promises made.
The design changes were made in record time, and by May of 2024 we had validated the new design changes in the Kirsten Wind Tunnel at the University of Washington in Seattle. This allowed us to not only show the design publicly for the first time at the AirVenture aviation celebration in Oshkosh, Wisconsin, in July of 2024, but also to push the design further into Production Engineering to ready the vehicle for production as soon as possible. The sequence of actions included building the first three production prototypes for testing at our existing R&D center in Oregon while we set up the major assembly plant and begin our major production.
Funding for the effort was increased in order to meet the more major goal of production engineering completed, and we raised more funds in 2024 than in any past year. We added four more staff and tripled our consulting engineering network to meet the demands. The supply chain was being built at the same time, with major suppliers for gas engine and electric motors selected along with many other parts.
Media efforts were energized as well, with our press releases from 2024 putting us in front of a total potential audience of over 1.6 billion people. Existing reservations represent a potential sales value of more than $485M. The new design was well received at AirVenture, and in case you haven’t seen the design of the production vehicle, a few of the latest images are included below.
New Design Renderings
Further Details of the New Design
If you want to geek out a bit on the new design, there are features haven’t been discussed significantly that can be talked about now. For instance, the radiators are located in the nose as it was found that we reduced drag by having the inlet be on the nose (highest pressure) with the outlet at the base of the windshield. As the air exits the radiator ducting there, it is split left and right so that the warmer, turbulent airflow from the radiators misses the engine bay air inlet scoop on the top of the roof behind the windshield. The high pressure of air being pushed upwards by the shape of the windshield re-attaches the airflow and adds to the decrease in drag that this location afforded us.
There is still a ‘frunk’ in the nose of the vehicle that can hold at least two overnight bags. We had a top hatch opening to access that in the last design. For this design we changed that to be side hatches, both left and right. The one on the side where the steering is located (this differs from country to country) will allow access to the steering mechanism and the remote electronics. The other side will allow access to the baggage area.
This keeps a clean look to the hood and reduces the problems for rainy day operations as the hatches don’t open upwards in a way that might allow rain to enter the frunk. The lower nose cone ahead of the frunk is removable to gain access to the front suspension and steering mechanism for maintenance. These hatches are protected against unauthorized entry and add to the security afforded this design to fully protect all flight and critical mechanisms while in ground mode.
The image above shows how we have shaped the body with a crease line to allow a two-tone paint scheme (for customers who want that). This new shape highlights the cockpit as a separate element, similar to many exotic sports cars. With the wider cockpit, occupants will have more elbow room and leg room. There is an angle increase to the seats to allow for a lower roof line necessary for drag reduction. We have built a plywood mockup of the floor/seat/roof and door opening to make sure that it is still easy to get in and out of. And we have tested to make sure that people who are over 6′ tall can still fit!
The carbon fiber parts making portion of our business is really taking off. We will probably be able to provide parts for other vehicles, whether driving or flying, as the robotic machinery we will be using has been improved over the last few years. We have also seen advances in materials that should allow us to build parts faster and at less cost than we had planned. Imagine a 3D printing-like process but with huge volume of materials applied to simplify and speed our parts making operations! Truly state of the art and high tech! We have also advanced our AI Co-Pilot, which can now talk with Air Traffic Control and soon will have other capabilities to help reduce pilot workload at busy airports.
Our Exciting Plans for 2025
In order to maximize the results from our build and test schedule, our goal is to run parallel paths for wing and body construction. Towards that end, we have already produced a portion of the molds for both body and wings and soon will start making parts from those molds. The mold making process will still go on for more than a month, as there are many molds to make. As mentioned, we will be building these first three production vehicles in our existing Oregon R&D facility. You can see the molds for the clamshell doors in the image below (built by the pros at Composite Approach in Redmond, Oregon).
Once the body is built and operationally tested, we plan to attach wings and tail and test the whole vehicle structurally. Once it has passed the structural testing, the vehicle will be cleared for flight testing. This is going to be a busy year, as once the flight tests confirm the wind tunnel results and establish our final vehicle specifications as to braking, acceleration, speed, cornering and flight performance and handling, we start to build two more production vehicles to round out our test program vehicles. We will continue testing these to try to find any weak points or parts while establishing our major production facility, with location to be decided in the next six months. To do this we will move any fixtures or assembly tooling to the new facility and establish both the assembly line and the carbon fiber parts manufacturing section that will eventually turn into our one-week Builder Assist Program. We will not likely finish the assembly plant setup until sometime in 2026, as that is a major undertaking.
I hope this has given you a fuller understanding of our many accomplishments in 2024 and our exciting plans for 2025! The momentum just keeps growing!
We have a Winning Advanced Air Mobility Program, and you could be part of it!
If you think that Joby and Archer are the biggest part of Advanced Air Mobility, you would be right if you only looked at the cash reserves they have. If you look at the infrastructure and scaling hurdles they face, you may get a different idea. Large cash is required for something like these two AAM vehicles, as they face not only FAA certification hurdles but also will be limited to operations out of existing airports and heliports, which indicates a very long road to success.
Why are landing places an issue? Can’t they land anywhere, as they don’t need a runway? The answer is that they have to operate safely the same as any other flying vehicle. And they produce noise, even if less than traditional helicopters. To get additional helipads or vertiports approved, you have to go through a process which includes public comment. We have all seen this process tie up new projects, even stop the ability of governments like California from building something as beneficial as light-rail transportation.
Perhaps in Future Cities built from the ground up to allow such transportation modes, we will see wider adoption of Vertical Take-Off and Landing (VTOL) vehicles. That is the future goal. For the present and up to many decades into the future, we will need to operate both on the ground and in the air, which is why we feel it is such a great idea to get in on companies like Samson Sky who are ready to produce vehicles that can be used today.
The VTOL works well to get around within a city that has sufficient landing places. In contrast, the Switchblade is for Regional Travel, taking passengers 500 miles at up to 160 mph, door-to-door. Enhanced by AI, the Switchblade has the capability to someday evolve into an autonomous vehicle that could pick people up via an app and drive and fly them to their final destination.
If you are an accredited investor, use our Investor Portal to review what we believe is our winning business plan to bring high-tech advanced transportation within the grasp of many people, and unleash the George Jetson in all of us.
Apply at: samsonsky.com/investors/
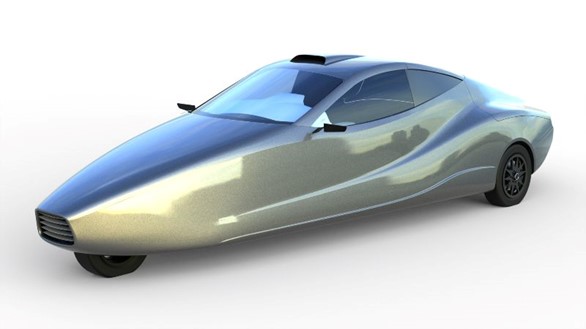
Latest Hot Press Coverage
Thomas Top Five
https://www.thomasnet.com/insights/thomas-top-five-2024/
Pretty cool to have the Switchblade Flying Car featured in the Thomas Insights Top Five Breakthroughs for 2024. Especially alongside the SpaceX Rocket Catch
Sam Bousfield
Captain, Switchblade Team